The art and function of adobe homes
Albuquerque Journal
9 Feb 2018
By GLEN ROSALES
Adobe bricks have superior insulating factors because of their mass. It’s a pretty simple recipe: take some of New Mexico’s finest dirt/clay, mix in some straw for authenticity and strength, pour into a mold and add water and plenty of sunshine.
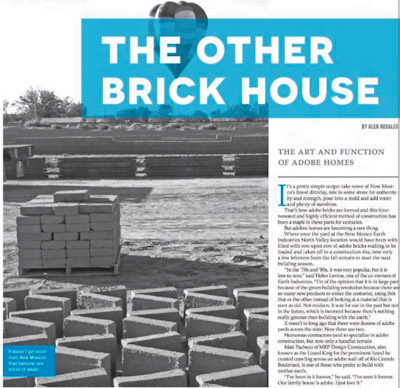
That’s how adobe bricks are formed and this time-honored and highly efficient method of construction has been a staple in these parts for centuries.
But adobe homes are becoming a rare thing. Where once the yard at the New Mexico Earth Industries North Valley location would have been with filled with row upon row of adobe bricks waiting to be loaded and taken off to a construction site, now only a few leftovers from the fall remain to start the next building season.
“In the ‘70s and ‘80s, it was very popular, but it is less so now,” said Helen Levine, one of the co-owners of Earth Industries. “I’m of the opinion that it is in large part because of the green building revolution because there are so many new products to entice the customer, using this that or the other instead of looking at a material that is seen as old. Not modern. It was for use in the past but not in the future, which is incorrect because there’s nothing really greener than building with the earth.”
It wasn’t too long ago that there were dozens of adobe yards across the state. Now there are two. Numerous contractors used to specialize in adobe construction, but now only a handful remain.
Matt Pacheco of MRP Design Construction, also known as the Lizard King for the prominent lizard he created crawling across an adobe wall off of Rio Grande Boulevard, is one of those who prefer to build with mother earth.
“I’ve been in it forever,” he said. “I’ve seen it forever. Our family house is adobe. I just love it.”
Adobe has an undeserved reputation for being difficult with which to work and expensive, Levine said. Bricks, however, cost about $1.50 apiece and a recent 2,000-square-foot home used about 2,500 bricks.
“There are not that many contractors who want to get their hands in the mud,” she said. “It takes longer to build an adobe house than it does to build a frame house.”
And there are other issues, added her brother and fellow owner Mark Levine.
“It is pretty labor intensive,” he admitted. “They weigh 30 pounds each and you’re mixing mud for every one either by hand or with a mixer. It’s all troweled on. It’s intensive work. You get out there with a wheelbarrow of mud and lay eight or 10 adobes and you’re like, ‘This is great.’ But at the end of the day when 1,200 adobes go through your hands, you say, ‘I got to do this tomorrow and the next day?’”
But while a frame house goes up relatively quickly, there are extra, time-consuming steps involved, as well.
“When guys do frame, they go bam, bam, bam and then they stand up the wall,” Mark Levine said. ‘But then they have to run their wiring through it. With adobes, you run that through the walls, which is another step saver there. The guys doing frame, they have to come back and do both sides, then insulate, plaster and finish the inside. You still have to wire and plaster the outside. All those things still exist. With adobe, you’ve already got a 10-inch solid wall. All the costs are the same.”
So the costs are really not that different. “And people are also afraid that it costs an exorbitant amount,” he said. “It can if you start getting fancy and wild, just like any other house. They don’t take that into account when you’re building the house because the adobe is such a minor portion of the cost of the house because it’s just the walls. People are misled by the contractors because they really don’t know adobe and they don’t want to do adobe.”
And the positives of adobe construction more than make up for any drawbacks.
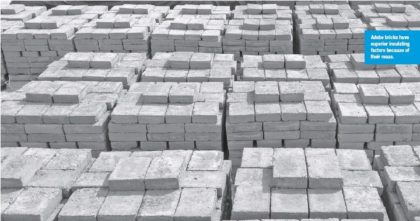
“It’s a fairly inexpensive product, a poor man’s product,” Pacheco said. “That’s why we love it so much because the poor man can afford it. But there’s a lot of laziness. It’s hard work. The bricks average 35 pounds a brick so you’re moving thousands of pounds of material a day just to get a portion up. Where the cost comes in is in time, because it takes longer to finish, but we’re trying to make it more cost effective. It should be cost effective. It takes more manpower. Framing is so quick. Our society has become a quick society that wants things done right away and as a fast as possible. This takes a little bit of time, but the end result is living in an environment that is sound proof, water proof, bullet proof. Once you’ve lived in one, you won’t feel comfortable in a frame home. They’re hollow.”
It works so well with a passive-solar theme, Helen Levine said. “With adobe, if you design the house so the sun can come in in the wintertime, the heat provided by the sun warms the mass,” she said. “It warms the mass of the floor and that of the walls as well. Then it’s stored in the walls and released at night when it’s cooler. Earth is ideal for that because it absorbs and releases slowly. Things like stone and concrete absorb also, but they release far too quickly.
And then it works in the summer time when cooling. If you open the house at night, so your windows are open at night, the cool air carries the remaining heat away and then the house stays cool during the day because you close the windows down so the hot air doesn’t come in.”
Too many people see adobes as a look instead of almost a lifestyle.
“At the bottom of my invoices I have a line that says, ‘Adobe, it’s more than just style,’” she said. “So many people think that adobe is just a style of construction with the flat roofs and stucco walls and things like that. But it’s a terrific material. Not only is it aesthetically pleasing and a comfortable material to live in, it’s quiet. People come here to the office, which is adobe, and they say ‘This place is so quiet and comfortable.’ Those are things you just don’t know unless you’ve lived in an adobe house.”